
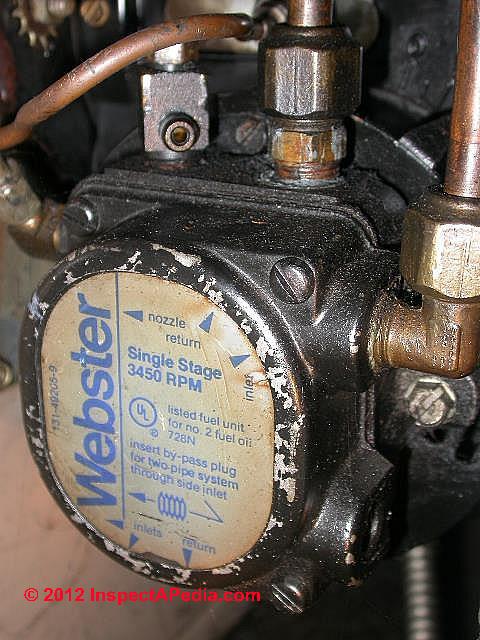
The existence of a particular regime may provide the desired results or it can deteriorate performance or cause reliability issues. The presence of a particular flow regime (bubble, stratified, slug, annular) within the pipe is a function of the volume fraction of the phases and their properties. Therefore, establishing the flow regime in the pipeline is of prime importance. Large bubbles or slugs are the usual suspects in the case of vibration of a pipeline carrying a gas-liquid mixture. What could cause vibrations in the pipeline? This article presents an analysis carried out using both conventional techniques and computational fluid dynamics (CFD), for determining the causes of vibrations in the transfer line exhibiting two-phase flow of vapour and liquid. During normal operation of the coker unit, the furnace outlet temperature is raised to about 500☌ and therefore the vapour flow rate at the outlet increases significantly due to vaporisation and mild cracking of vacuum residue even at higher pressures of 3.5-6.0 kg/cm2(g).ĭuring a start-up operation of the DCU, the transfer line experienced vibrations, giving rise to safety and reliability concerns. After establishing the desired flow circulation, the header is disconnected from the fractionator and connected to the coker drum. The vacuum residue and steam mixture at the furnace outlet enters a transfer line connected to a header, which is connected to the fractionator during start-up for closed loop circulation at a temperature of 300-350☌ and a pressure of 1.5-3.0 kg/cm2(g).

Steam is added along with vacuum residue in the furnace to create additional turbulence for better heat transfer and to avoid coking inside the heater tubes.įigure 1 depicts the flow scheme for a vacuum residue and steam mixture during start-up and normal operation of the DCU.

#Furnace j line cracked
Vacuum residue is first heated in a furnace to about 500☌ for a very short time, to avoid coking inside the furnace tubes, and then cracked inside the coke drum, where sufficient reaction time is provided. The delayed coking unit (DCU) takes vacuum residue as feed and thermally cracks it into useful lighter products such as liquefied petroleum gas (LPG), naphtha, gas oils and residual coke. Delayed coking is an important process in a petroleum refinery and adds significantly to the gross refining margin.
